Wo Nullen und Einsen fliegen lernen
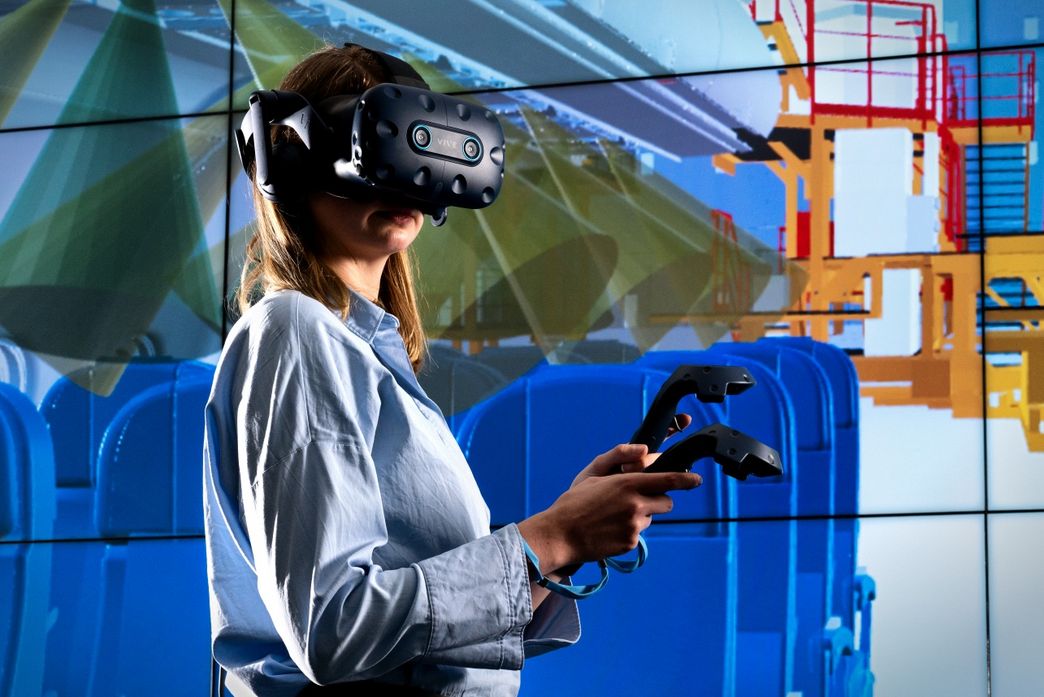
In einer neuen Fabrik sollen neue Konzepte und Technologien für Flugzeuge bewertet und getestet werden. Das Besondere an ihr: Sie passt auf wenige Quadratmeter, denn sie ist digital. Ein gemeinsames Projekt des DLR und Airbus.
Wasserstoff oder synthetisches Kerosin? Die Frage, mit welchem Energieträger zukünftige Flugzeuge angetrieben werden, ist eine der drängendsten in der Luftfahrt. Die physikalischen Größen wie Masse, Widerstand, Energieeffizienz oder Klimawirkung, die wichtig sind, um die Frage aus flugmechanischer Sicht zu betrachten, werden bereits im Zusammenspiel der Fachinstitute des DLR berechnet. Doch die Parameter allein erlauben keine Aussage über das tatsächliche Potenzial einer Technologie. Das hängt auch davon ab, wie wirtschaftlich sie als industrielles Produkt produziert werden kann.
Simulationen dienen als Blick in die Zukunft
Wie aufwändig es ist, die Fertigungsprozesse von Verkehrsflugzeugen auf neue Technologien anzupassen – beispielsweise veränderte Tanks oder Antriebe –, lässt sich nicht zuverlässig bewerten. Dazu sind die Fertigungssysteme viel zu komplex. Hinzu kommt, dass die Randbedingungen der industriellen Produktion teilweise der Geheimhaltung unterliegen. Entsprechend können Forscherinnen und Forscher die exakten Anforderungen nur teilweise in ihrer Arbeit berücksichtigen. Im Rahmen des Projekts Effizienzsteigerung in der Produktionsplanung und -Steuerung durch Präskriptive Analytik (EPSIA), das vom Bundesministerium für Wirtschaft und Klimaschutz gefördert wird, entwickeln das DLR und der Flugzeughersteller Airbus gemeinsam eine digitale Fabrikumgebung. In dieser Digital Launch Factory kann das DLR als virtueller Hersteller die Industrialisierbarkeit neuer Luftfahrzeuge bewerten.
Energieeffizient und klimaneutral
Ein Ziel, das sich die deutsche Bundesregierung im Einklang mit dem Green Deal der Europäischen Kommission gesetzt hat, ist, den Klimaschutz im Luftverkehr wirksam umzusetzen und die dafür notwendigen Technologien zur Marktreife zu bringen. Bis 2050 soll der Luftverkehr klimaneutral und nachhaltig sein. Dazu sollte der Energieverbrauch der Flugzeuge bis dahin halbiert werden. Das bedeutet auch, dass sich zukünftige Flugzeugkonfigurationen deutlich von ihrem heutigen Aussehen unterscheiden werden. Für die äußere Form können das etwa höher gestreckte Flügel oder neue Antriebskonzepte sein. Der innere Aufbau muss Platz für klimaneutrale Technologien wie Wasserstofftanks, Brennstoffzellen und Batterien bieten.
Das DLR-Institut für Systemarchitekturen in der Luftfahrt
Das DLR-Institut für Systemarchitekturen in der Luftfahrt
In Hamburg arbeiten derzeit 60 Mitarbeiterinnen und Mitarbeiter daran, wie neue Luftfahrzeuge und deren Komponenten in Zukunft leistungsfähiger, effizienter und sicherer werden können. Im Fokus ihrer Forschung steht das „virtuelle Produkt“, bei dem alle Eigenschaften des Flugzeugs über Entwurf, Erprobung, Herstellung und Zertifizierung virtuell dargestellt werden. Bei diesem Verfahren werden verschiedene Teilsysteme zu einem Gesamtsystem miteinander gekoppelt. Die Kombination der Teilsysteme wird als Systemarchitektur bezeichnet. In ihrer Arbeit untersuchen die Wissenschaftlerinnen und Wissenschaftler sowohl die einzelnen Systeme als auch deren Wechselwirkungen.
Klimaschutz endet aber nicht bei innovativen Flugzeugkonzepten, die neue Technologien und Bauweisen erfordern, auch die Produktion selbst soll grüner werden: Sie liefert mit energieeffizienten und nachhaltigen Fertigungsprozessen einen wichtigen Beitrag. Deshalb erstellt das Team der Digital Launch Factory unter anderem Simulationen für die Montage der wichtigsten Flugzeugkomponenten. Diese können an verschiedene Konfigurationen angepasst werden. Die Berechnungen zeigen auch, inwiefern Energie- und Materialaufwände sinken oder steigen beziehungsweise inwieweit ein geschlossener Materialkreislauf realisiert werden kann. Werden neue Produktarchitekturen oder Fertigungsverfahren entwickelt oder vorhandene modifiziert, können neue Simulationen in die virtuelle Fabrik eingebunden werden. Daran forschen Wissenschaftlerinnen und Wissenschaftler beispielsweise im DLR-Querschnittsprojekt Factory of the Future (FOF-X).
Agile und modulare Fertigung
Das Team in Hamburg legt einen Schwerpunkt auf industrielle Aspekte, die dem deutschen Wertschöpfungsanteil heutiger Luftfahrtprodukte entsprechen – beispielsweise die Integration von Kabine und Systemen in den Flugzeugrumpf. Bisher wird zunächst der Rumpf gefertigt, dann werden die Subsysteme integriert und zum Schluss die Kabinenmonumente montiert. Bei einem Ansatz, den die DLR-Forscherinnen und -Forscher verfolgen, werden die Subsysteme in vormontierte Baugruppen der Kabine integriert. Ein Beispiel dafür ist das Crown-Modul, das alle Systeme und Kabinenkomponenten oberhalb der Fensterreihe beinhaltet. Dazu gehören die Gepäckablage, das Deckenpanel und die Rohre der Klimaanalage. Der Zulieferer verschickt die vorgefertigten Module, wodurch sich auch die Anzahl der Bauteile reduziert, die zeitgleich in das Flugzeug eingebaut werden müssen. Da nicht abgewartet werden muss, bis der Rumpf fertig produziert ist, verkürzt sich die Montagezeit im Flugzeug mit dieser neuen Methode erheblich. Auch die Zeit für das aufwändige Ausrichten der einzelnen Verkleidungselemente wird verringert. Somit beeinflusst das Design der Flugzeugkabine unmittelbar die Produktionsweise. DLR-Wissenschaftlerinnen und -Wissenschaftler forschen daran, Kabinen unter den Randbedingungen einer effizienten Industrialisierung so zu gestalten, dass sie sicher, komfortabel und individualisierbar sind. Für Herstellerfirmen ist die Individualisierbarkeit der Kabinen ein entscheidendes Verkaufsargument.
Aber in der Digital Launch Factory ist nicht alles digital: Teilaspekte werden real im Labor aufgebaut – gemeinsam mit Airbus, Diehl und anderen Industriepartnern im Zentrum für Angewandte Luftfahrtforschung Hamburg ZAL. Dazu gehört eine robotergestützte Vormontagestation. Hier testen die Fachleute, wie kollaborative Roboter die Systeme automatisiert in die Baugruppenmodule einbauen. Die Ergebnisse fließen direkt in die Algorithmen der digitalisierten Fabrik. Das ist ein erster Schritt in Richtung Industrie 4.0, bei der virtuelle und reale Welt miteinander vernetzt sind. In gemeinsamen Projekten mit Europas größten Flugzeugherstellern lassen sich die Baugruppen, wie das Crown-Modul, zunächst real und automatisiert vormontieren und die Abläufe dann mithilfe der virtuellen Fabrik auf die gesamte Produktion hochskalieren. Die reale Vormontage im Vorfeld ist wichtig, damit die Wissenschaftlerinnen und Wissenschaftler die digitale Fabrik mithilfe dieser Daten validieren können.
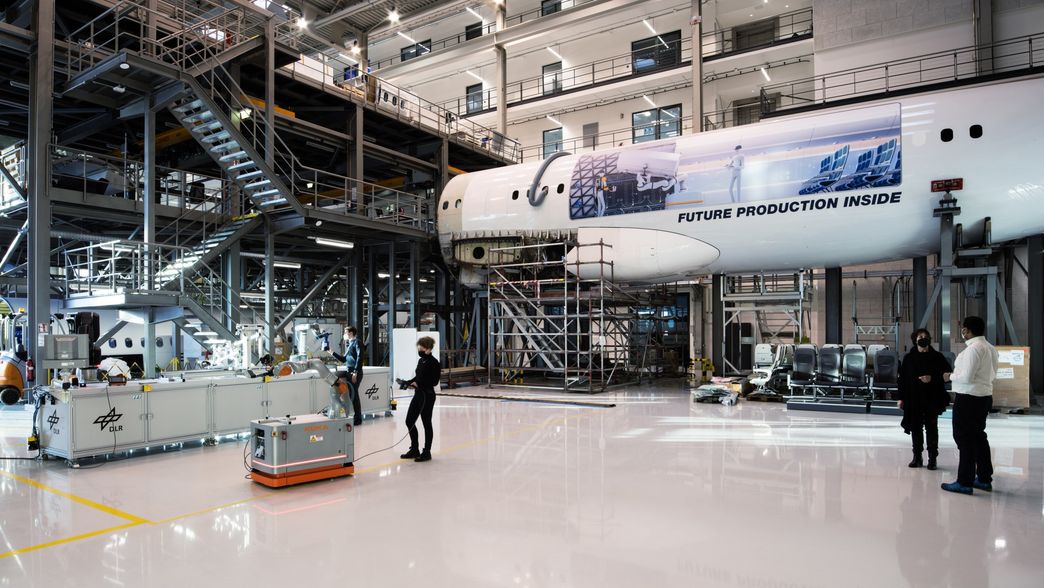
Wechselseitiger Austausch im gesamten Lebenszyklus
Ein weiteres Ziel der Digital Launch Factory ist es, Expertinnen und Experten vom Entwurf bis zur Produktion zu vernetzen. Werden der Entwurf eines Produkts und dessen Produktion in allen Entwicklungsphasen simultan betrachtet, spricht man von Co-Design. Es minimiert aufwändige Nachbesserungen des Produktdesigns während der Fertigung. Außerdem betrachtet die Methode Fertigungsaspekte schon im Entwurf neuer Flugzeugkonfiguration. Die Vorteile des Co-Designs machen es zu einem zentralen Forschungsthema in der deutschen Luftfahrtindustrie. Im Zuge der Digitalisierung werden Daten, Modelle und Werkzeuge konsequenter verwendet.
Die Digital Launch Factory ist ein entscheidender Baustein, mit dem das DLR die Luftfahrt als Gesamtsystem modellieren und erforschen kann. Revolutionäre Änderungen wie das klimaneutrale Fliegen können nur dann effizient umgesetzt werden, wenn Entwurf, Industrialisierung und Betrieb synergetisch aufeinander abgestimmt sind. Dazu ist der erste Schritt für die Wissenschaftlerinnen und Wissenschaftler in Hamburg, alle relevanten DLR-Institute sowie die Industriepartner an einen Tisch zu bringen und dort gemeinsam die Wechselwirkungen zwischen dem Produkt Flugzeug und dessen Fertigung genau unter die Lupe zu nehmen.
Autor: Dr. Björn Nagel (Gründungsdirektor des DLR-Instituts für Systemarchitekturen in der Luftfahrt)
Dieser Artikel ist zuerst im DLRmagazin 170 des Deutschen Zentrums für Luft- und Raumfahrt erschienen.